Hydraulische vertikale Metallballenpressen üben vertikale Abwärtskraft und Druck aus, um verschiedene Materialien zu komprimieren. Sie können eine Reihe von Gegenständen wie Pappe, Papier, Textilien, Dosen, Kunststoffe und Nichteisenmetalle effektiv zu Ballen pressen. Die Materialien werden kalt zu dichten rechteckigen Blöcken gepresst, was die Lagerung und den Transport erleichtert.
Unter den verschiedenen Ballenpressentypen sind Vertikalballenpressen die kostengünstigsten, nehmen den geringsten Platz in einer Anlage ein und sind einfach und sicher zu bedienen. Sie können Ballen in den Größen 24, 30, 36, 48, 60 und 72 Zoll produzieren. Der Produktionsprozess umfasst das Laden des Materials durch den Bediener, das Betätigen des Kolbens und das Binden der Ballen.
Welches Material können Sie in hydraulischen Metallballenpressen verarbeiten?
Diese Ballenpresse ist für ihre Vielseitigkeit bekannt und kann eine Vielzahl von Materialien verarbeiten, wie z. B. Wellpappe, Zeitungspapier, PET-Kunststoffflaschen, HDPE-Kunststoffe, Aluminiumdosen, Blechdosen, Stahldosen, Autoabfälle, Produktionsabfälle, Bauschutt, Schrumpffolien usw. Verpackungen, Kunststofffolien, Stoffe und Textilien.
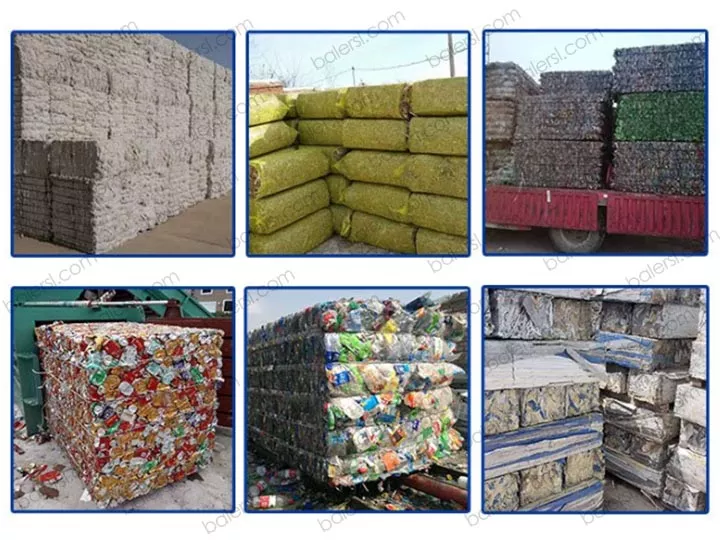
Wer profitiert von vertikalen Metallschrottballenpressen?
Eine vertikale hydraulische Ballenpresse ist in erster Linie zum Komprimieren und Ballenpressen verschiedener Arten von losen, feinen oder Abfallmaterialien konzipiert. Diese Ausrüstung findet in zahlreichen Branchen breite Anwendung, darunter Altpapier, Kunststoffe, Metallabfälle und Stoffe.
Zu den Hauptnutzern zählen große Einzelhandelsgeschäfte, Kioske, Schulen, Lagerhäuser, Krankenhäuser, Apotheken, Vertriebszentren, Lebensmittelgeschäfte, Einzelhändler, Recyclingunternehmen, Produktionsstätten, Nichteisen-Schrottplätze, kommunale Recyclinganlagen, Einkaufszentren, Supermärkte und Hotels.
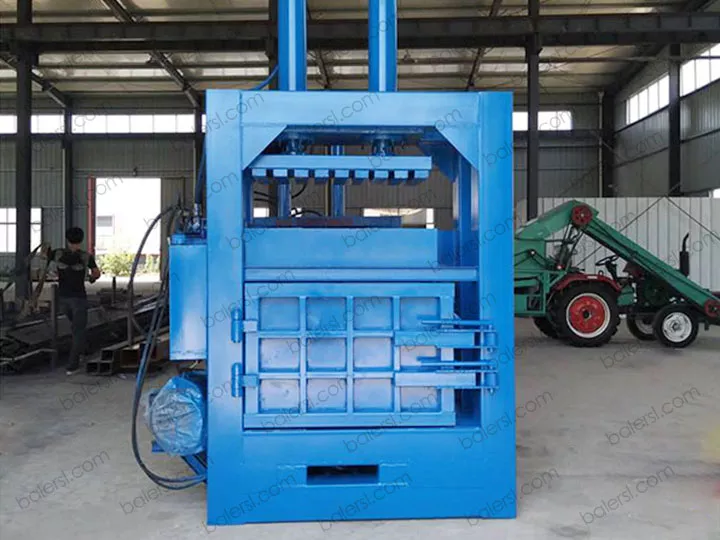
Vorteile der Ballenpressung und des Recyclings von Industrieabfällen
- Kosten senken – Sparen Sie Geld, indem Sie die Entsorgungskosten senken.
- Platz optimieren – weniger Unordnung und weniger Stolperfallen.
- Steigern Sie den Umsatz – Geld verdienen, indem Sie Papierballen an Papierfabriken verkaufen.
- Energieeinsparungen und -reduzierung – Durch das Recycling von Aluminiumprodukten können beispielsweise rund 951 TP3T Energie eingespart werden.
Komponenten der Schrottballenpresse
Die Schrottballenpresse besteht im Wesentlichen aus folgenden Komponenten:
- Hydrauliksystem: Bietet starken Druck, um die Kompressionskraft beim Metallballenpressen zu erreichen.
- Rahmen und Trichter: Stützen und fixieren Sie das Metallmaterial, damit es gepresst und gepresst werden kann.
- Hydraulikzylinder und Kolben: Drücken Sie den Kolben durch hydraulischen Druck an den Rahmen. Üben Sie außerdem Druck aus, um das Metallmaterial in eine kompakte Form zu pressen.
- Bedienfeld: Wird verwendet, um den Betrieb und die Parametereinstellung der vertikalen Metallballenpresse zu steuern und Parameter wie Druck und Ballenpresszeit anzupassen.
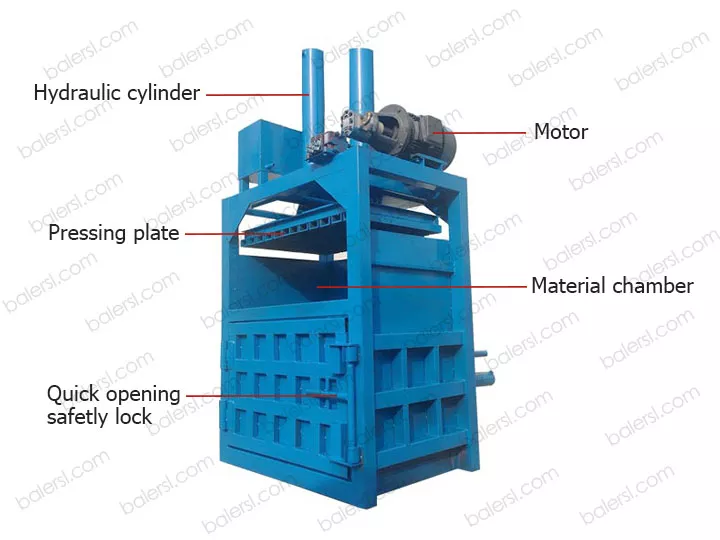
Funktionsprinzip des vertikalen Metallverdichters
Vorbereitung
Wiederverwertbare Gegenstände werden in die Ballenpresskammer geladen, um eine sichere und ordnungsgemäße Platzierung zu gewährleisten.
Starten Sie die Ballenpresse
Das Hydrauliksystem wird über das Bedienfeld gestartet, sodass die Hydraulikzylinder und -kolben der vertikalen Metallballenpresse zu arbeiten beginnen.
Komprimierungsprozess
Der Hydraulikzylinder drückt den Kolben nach unten, um Druck auszuüben. Eine Platte am Ende des Hydraulikzylinders komprimiert das Material, bis die gewünschte Ballengröße erreicht ist.
Ballenpressen beenden
Sobald der voreingestellte Ballenpresszustand erreicht ist, stellt das Hydrauliksystem den Betrieb ein und der Ballenpressen ist beendet. Anschließend werden die Ballen mit Draht oder Umreifungsband zusammengebunden.
Entladungsmethode
Je nach Bedarf entlädt die vertikale Metallballenpresse die gepressten Metallstücke auf unterschiedliche Weise. Sie können zwischen manuellem und automatischem Entlademodus wählen.
Die Größe und das Gewicht der aus einer Ballenpresse austretenden Wertstoffblöcke variieren je nach Größe der verwendeten Ballenpresse.
Entlademethoden von Altballenpressen
Vertikal Schrott Ballenpressen verfügen über unterschiedliche Entladungsmethoden. Kunden können den erforderlichen Modus entsprechend ihren Anforderungen auswählen.
- Manuelle Entladung: Der Bediener entfernt die gepressten Metallblöcke manuell aus der Ballenpresse, was für kleinere Produktionsmengen und Betriebsräume geeignet ist.
- Automatische Entladung: Die gepressten Metallblöcke werden durch das automatische Fördersystem, das für die Massenproduktion und den Dauerbetrieb geeignet ist, automatisch zum vorgesehenen Ort transportiert.
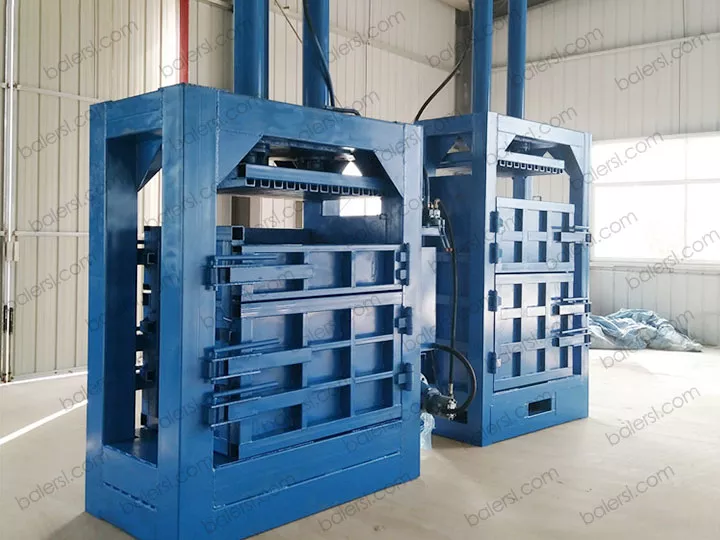
Vorteile der hydraulischen Blechballenpresse
- Im Vergleich zu horizontalen Ballenpressen sind vertikale Schrottballenpressen hinsichtlich des Platzbedarfs kompakter und eignen sich für begrenzte Platzverhältnisse.
- Es besteht aus hochfestem Stahl und hydraulischen Teilen und bietet eine hervorragende Tragfähigkeit und Haltbarkeit.
- Je nach Bedarf können Sie zwischen manuellen oder automatischen Entlademethoden wählen, sind hoch flexibel und können sich an unterschiedliche Arbeitsumgebungen anpassen.
- Die Materialbox verfügt über einen drehbaren, geschlossenen Deckel, der eine große Öffnungsfläche bietet, die das Einfüllen großer, leerer und dünner Materialien besonders einfach macht.
- Alle beweglichen Komponenten arbeiten mit hydraulischem Druck und sorgen so für stabile Leistung, hohen Packdruck, sicheres Bündeln und effizientes Packen.
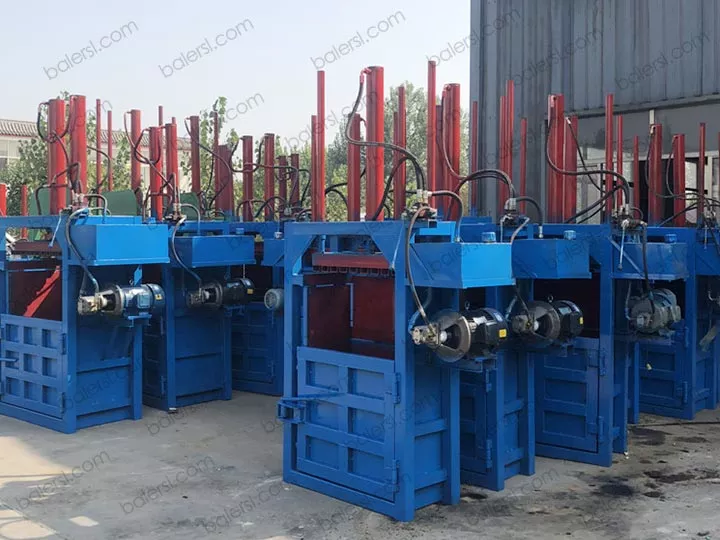
Technische Daten der vertikalen Metallballenpresse
Modell | SLV-15 | SLV-30 | SLV-60 | SLV-80 | SLV-120 |
Druck | 15T | 30T | 60T | 80T | 120T |
Leistung | 5,5–7,5 kW | 5,5 kW | 7,5 kW | 11KW | 18,5 kW |
Kapazität | 0,6–0,8 t/h | 0,8–1 t/h | 1,5–2 t/h | 2-3T/Std | 4–5 t/h |
Ballengewicht | 20–40 kg | 100 kg | 300 kg | 400-500 kg | 400-600 kg |
Ballengröße | 600*400*200-500mm | 800*400*600mm | 900*600*800mm | 1100*800*1000 mm | 1200*800*12 00mm |
Maschine Gewicht | 1TON | 1,2 TONNEN | 1,5 TONNEN | 2TON | 3,2 TONNEN |
Außerdem hat Shuliy horizontale Ballenpressen aus Metall um den unterschiedlichen Bedürfnissen der Kunden gerecht zu werden. Wir sind ein führender Technologieinnovator in der Recycling- und Abfallverarbeitungsbranche. Kaufen Sie eine vertikale Ballenpresse für Ihre Wertstoffe und wir unterstützen Sie bei der Auswahl der perfekten Ballenpresse für Ihre Geschäftsanforderungen.